Sustainability is an increasingly recognised value – and laboratories around the world are taking action to try to reduce their ecological footprint as much as possible.
Integra Therapeutics, a UPF spin-off dedicated to the development of a new genetic engineering tool, recently became the first institution in the Barcelona Biomedical Research Park (PRBB) to receive an official sustainability certification from My green lab. This certification programme, of which the company has received Platinum level (the second of three levels), recognises laboratories that follow sustainable practices.
My green lab started as a charity to train scientific staff to improve sustainable aspects of the laboratory. From there it has gone on to create an ambassadors network. Natalia Artigas, a member of Integra Therapeutics, is one of its ambassadors; she received the training, and is now part of the PRBB sustainability group, where she shares this information and the tools learned.
In addition to training scientific staff, My green lab currently has a certification programme for organisations. We talked to Natalia about how the spin-off located on the 7th floor of the PRBB has become the first company resident in the park to be certified in sustainability.
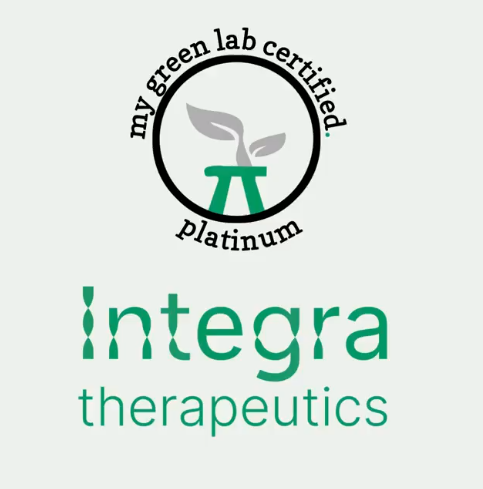
What has the certification consisted of?
At My green lab they are very lab focused, they understand very well how labs work. So the first thing they do is to ask you a lot of questions about the technical equipment you have and show you how to improve the energy efficiency of that particular equipment. They also ask about things that go beyond the particular lab, questions relevant to the infrastructure of the building, e.g. do all the taps have water-saving dispensers? Are the lights in the building LED? In this sense, being in the PRBB has helped, because the building has many of these good practices already in place.
Being in the PRBB has helped to achieve the certification, because the building has many of the sustainable best practices already in place. Natalia Artigas (Integra Therapeutics)
How does the process work?
First they make you answer a test to see how the laboratory works. Then they give you advice on what changes can be made to improve. Once the changes have been made, they test you again – each person involved in the lab is tested individually, to compare the practices of the different lab members. Finally, you are given a final score and a certification level: Green, Platinum or Gold.
How long does the whole process take and what did you do to achieve it?
It took us about 9 months. After the initial assessment and receiving advice on things to change, we held monthly meetings in which we dealt with the different issues: community, recycling, shopping, chemicals, water… Up to 9 topics that we had been assessed on. In these meetings, we organised ourselves, we divided up the tasks of looking for information, etc. It was very good because everyone wanted to collaborate, the whole laboratory was very active, came to the meetings and there was a very good response.
Can you give us some examples of things you have changed?
One very interesting thing we did was a ‘waste audit‘ – which is to keep all the waste from the lab for a week and sort through it to see how to improve this waste management. The first thing you look at is whether the waste is going to the right place – e.g. sometimes things are thrown in the biohazard waste bin that don’t really need to go there. And that means an extra cost both environmentally and economically, because the biohazard waste receives a much more complex treatment… It’s a very recommendable exercise, because sometimes you are surprised by what you throw there!
Then, among the things that go into biohazards, we looked at what plastics we could replace. Something we had already done, for example, was to replace the plastic bacterial growth tubes with glass ones, which can be autoclaved (sterilised) and reused.
Another important thing, which seems obvious, is to check your reagents regularly to prevent them from expiring. In fact, this is a big issue; Sigma has found that 5% of the products they sell are thrown away without ever being used! Simply because they have expired. That’s why it’s essential to keep good records of what you have, use first the ones that are going to expire soon… and, above all, share reagents with others!
And about the reagents, apart from the expiry date, they also look at what chemicals you use. This is something we often don’t think about – you use the default reagents, the ones that have always been used. But nowadays, “green chemistry” is very much in vogue, and this is all about replacing reagents that are harmful to the environment with less harmful substitutes.
What about energy?
The energy consumption of machinery is probably the one with the biggest impact. It is important to be aware of when they are switched on unnecessarily – apart from the fact that it also affects the lifetime of the machine! So one thing we do now is to rotate between lab members to ensure that machines are switched off at night, as well as checking the maintenance of all machines.
Interestingly, the machinery that wastes the most energy are laminar flow cabinets, because if you don’t close it, the cabinet keeps generating a flow continuously… So the only thing you have to do is close it when you finish using it! But often it’s not done because of carelessness, laziness, or because you want it to be ready when you need it again… I know that some labs in the UK have put in automatic systems that detect when there are no people and it closes automatically, saving a lot of energy.
Obviously, adjusting the temperature of freezers is another big step that can have a big effect – plus you make the change once and then can forget about it! To do this, we first analysed the efficiency of our freezer. With a go-pro camera, a student in the lab, Albert, took pictures of the freezer temperature every minute, to see how it varied when you opened it, how it recovered, etc… He then did an analysis of the temperature fluctuations and we saw that the biggest impact was the time you kept the door open, not so much the number of times you opened it. So it was feasible to make the temperature change from -80ºC to -75ºC if we avoided keeping the door open too long. By improving practices, we were able to raise the temperature without putting our samples at risk, and now all MELIS-UPF freezers have made this change! Our next goal will be to go from -75°C to -70°C…
Any other important subjects?
Yes, water! In the building we use water with different degrees of purity: normal, distilled, and ultrapure water (Millipore). Sometimes ultrapure water is used, when in fact distilled water would be enough. And, as we have seen with waste, generating ultrapure water is much more expensive than generating distilled water (it takes 6-7 litres of decalcified water to generate 1 litre of ultrapure water, whereas 1 litre of distilled water requires only 3 litres of normal water).
Until recently, we used to buy ultrapure water – but now we generate it right here at the PRBB, in Millipore machines that are on every floor of the building. And it’s the same quality as the purchased water. We eliminate the CO2 associated with transport, plastics, and also, at PRBB the water used to make ultrapure water is not wasted, but is reused for flushing toilets.
At PRBB the water used to obtain ultrapure water is reused for flushing the toilets.
Waste, reagents, machinery, water… What has been the main challenge?
I thought it would be recruiting people from the group to collaborate, but that turned out to be the easiest! I’m super grateful to the whole team.
The biggest challenge has perhaps been at the purchasing level because it does not depend only on us. For example, to reduce CO2 associated with transport, and parcels, we made the effort to wait so we could buy more things at once from the same supplier; we made sure we ordered them enough time in advance not to run off… but then, even though we ordered everything at the same time, they sent it to us in three different packages! They assume that you want to have it as soon as possible, which is understandable. So, if they have one product and the other two are missing, they send you the first one. It’s a bit frustrating, but you just have to talk to the company and explain that you want them to send it all together, rather than as soon as they have some products.
What does it mean for you to have this certification?
It is aligned with company policy. We are a young company, and our CEO, Avencia Sánchez-Mejías, was very keen to do things right from the beginning. She was the one who told me about the PRBB sustainability group as soon as I arrived at Integra.
Having the accreditation gives you a guide of what you have to change and how, because sometimes you have the will to do it but you don’t know where to start! They categorise everything and help you step by step.
Finally, a tip for other groups or institutions that want to become more sustainable.
First, join existing sustainability groups, such as the one at the PRBB. Because there is a lot of knowledge and resources there. And we need people, because there are few of us who are very active, since you have to combine your laboratory work with improving sustainability, and not everyone has the same availability… Everything takes time, and we do it all on a voluntary basis. In my case, I am lucky to have the support of my boss to dedicate time to it. It also helps if you do the My green lab course – and that doesn’t take a lot of time!
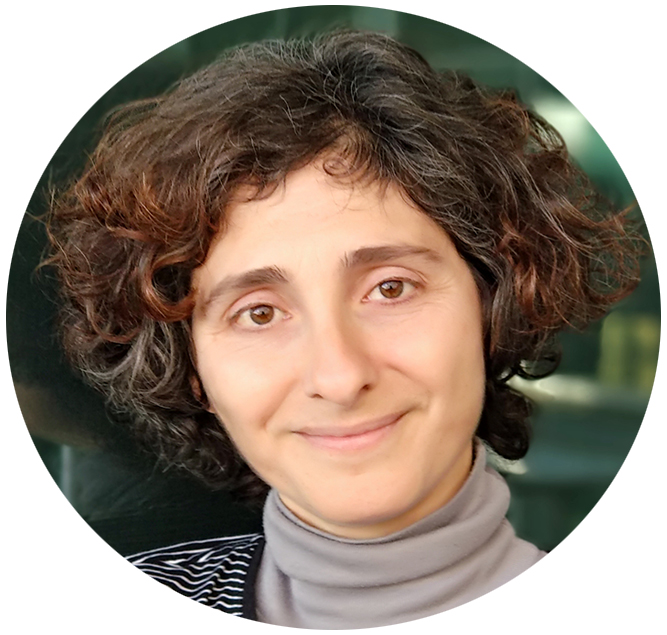