La sostenibilidad es un valor cada vez más reconocido – y los laboratorios de todo el mundo se están poniendo las pilas para intentar reducir al máximo sus huellas ecológicas.
Integra Therapeutics, una spin-off de la UPF dedicada al desarrollo de una nueva herramienta de ingeniería genética, se ha convertido recientemente en la primera institución del Parque de Investigación Biomédica de Barcelona (PRBB) en recibir la certificación de sostenibilidad oficial de My green lab. Este programa de certificación, del que la empresa ha recibido el nivel Platinum (el segundo de tres niveles), legitima a los laboratorios que siguen prácticas sostenibles.
My green lab nació como una organización benéfica para formar a personal científico en la mejora de aspectos sostenibles del laboratorio. De ahí ha ido creando una red de embajadores. Natalia Artigas, miembro de Integra Therapeutics, es una de sus embajadoras; recibió la formación, y ahora forma parte del grupo de sostenibilidad del PRBB, donde comparte esta información y las herramientas aprendidas.
Además de la formación a personal científico, actualmente My green lab tiene un programa de certificados para organizaciones. Hablamos con Natalia sobre cómo esta spin-off localizada en la 7ª planta del PRBB se ha convertido en la primera empresa residente en el parque en certificarse en sostenibilidad.
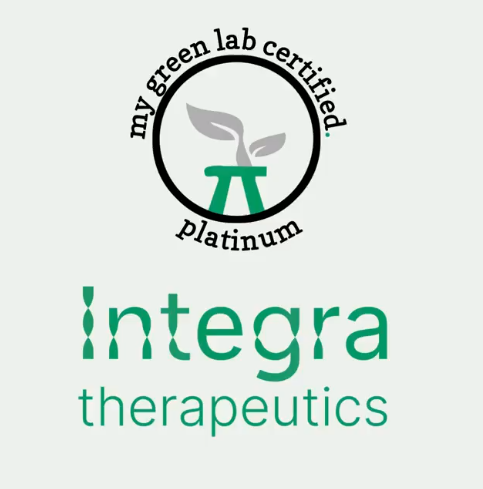
¿En què ha consistido la certificación?
En My green lab estan muy enfocados en el laboratorio, entienden muy bien cómo funcionan. Así que lo primero que hacen es hacerte un montón de preguntas sobre el equipo técnico que tienes y te enseñan como mejorar el gasto energético de ese equipo en concreto. También preguntan sobre cosas que van más allá del laboratorio particular, cuestiones relevantes a las infraestructuras del edificio, e.g. ¿tienen todos los grifos dispensadores de ahorro de agua? ¿Son LED las luces del edificio? En este sentido, estar en el PRBB ha ayudado, porque el edificio tiene muchas de estas buenas prácticas ya establecidas.
Estar en el PRBB ha ayudado a conseguir la certificación, porque el edificio tiene muchas de las buenas prácticas sostenibles ya establecidas
Natalia Artigas (Integra Therapeutics)
¿Cómo funciona el proceso?
Primero te hacen un test para ver cómo funciona el laboratorio. Luego te dan los consejos de qué cambios se pueden hacer para mejorar. Una vez hechos los cambios, te vuelven a hacer el test – a cada persona que participa del laboratorio individualmente, para contrastar las prácticas de los diferentes miembros del laboratorio. Finalmente, te dan una puntuación final y un nivel de certificación: Green, Platinum o Gold.
¿Cuánto tarda todo el proceso y cómo os habéis organizado?
Nosotros tardamos unos 9 meses. Después de la valoración inicial y recibir los consejos de cosas a cambiar, hicimos reuniones mensuales en las que íbamos tratando los distintos temas: comunidad, reciclaje, compras, químicos, agua… Hasta 9 temáticas que nos habían valorado. Ahí nos organizábamos, nos repartíamos las tareas de buscar información, etc. Ha estado muy bien porque todo el mundo quería colaborar, venía a las reuniones, todo el laboratorio ha sido muy activo y ha habido muy buena respuesta.
¿Puedes darnos algún ejemplo de qué cosas habéis cambiado?
Una cosa muy interesante que hicimos fue una ‘auditoría de residuos’ – que consiste en guardar toda la basura del laboratorio durante una semana y clasificarla para ver cómo mejorar esta gestión de residuos. Lo primero que se mira es si la basura está yendo al lugar adecuado – e.g. a veces se tiran cosas a la basura de biohazards (restos biológicos peligrosos) que no haría falta que fueran ahí. Y eso supone un coste extra tanto ambiental como económico, porque estos residuos reciben un tratamiento mucho más complejo… Es un ejercicio muy recomendable, porque ¡a veces te sorprendes de lo que tiramos ahí!
Después, dentro de las cosas que van a biohazards, miramos qué plásticos podíamos sustituir. Algo que ya habíamos hecho nosotros, por ejemplo, era sustituir los tubos de crecimiento bacteriano de plástico por unos de cristal, que se pueden autoclavar (esterilizar) y reutilizar.
Otra cosa importante, que parece obvia, es revisar los reactivos para evitar que caduquen. De hecho, esto es un gran tema; la empresa Sigma ha detectado que el 5% de los productos que venden se tiran directamente ¡sin haberlos usado! Simplemente porque han caducado antes de usarlos. Por eso es esencial hacer un buen registro de lo que tienes, usar primero los que van a caducar antes… y, sobre todo, ¡tener reactivos comunes!
Y sobre los reactivos, aparte de la fecha de caducidad, también miran qué productos químicos usas. Esto es algo que a menudo no pensamos – usas los reactivos por defecto, los que siempre se han usado. Pero actualmente está muy en auge la “química verde” (Green chemistry) que consiste en cambiar los reactivos que son nocivos para el medio ambiente por sustitutos menos nocivos.
¿Y a nivel energético?
El gasto energético de la maquinaria es seguramente el de mayor impacto. Es importante ser conscientes de cuando están encendidas sin necesidad – aparte de que también afecta a la vida útil de la máquina… Por eso una cosa que hacemos es rotaciones entre los miembros del lab para asegurar que las máquinas quedan apagadas de noche, así como confirmar el mantenimiento de todas las máquinas.
Curiosamente la maquinaria que más energía gasta son las cabinas de flujo laminar, porque si no la cierras, la cabina sigue generando un flujo continuamente… ¡Así que lo único que hay que hacer es cerrarla al acabar de usarla! Pero a menudo no se hace por descuido, pereza, o porque quieres que esté preparada cuando la vuelvas a necesitar… Sé que en algunos laboratorios del Reino Unido han puesto cierres automáticos que detectan cuando no hay gente y se cierra automáticamente, y así se ahorra mucha energía.
Obviamente, ajustar la temperatura de los congeladores es otro gran paso que puede tener un gran efecto – además ¡haces el cambio una vez y ya te olvidas! Para hacerlo, nosotros primero analizamos la eficiencia de nuestro ultracongelador. Con una cámara go-pro, un estudiante del laboratorio, Albert, hizo fotos de la temperatura del congelador cada minuto, para ver cómo variaba al abrirlo, cómo se recuperaba etc… Luego hizo un análisis de las fluctuaciones de la temperatura y vimos que el mayor impacto lo tenía el tiempo que mantuvieras la puerta abierta, pero no las veces que la abrieras, de manera que era factible hacer el cambio de temperatura de -80ºC a -75ºC si evitábamos tener la puerta abierta demasiado tiempo. Así, mejorando las prácticas, pudimos subir la temperatura sin poner en riesgo nuestras muestras. ¡Ahora todos los ultracongeladores del MELIS-UPF han hecho este cambio! Nuestro siguiente objetivo será pasar de -75ºC a -70ºC…
¿Algún otro tema importante?
¡Sí, el agua! En el edificio usamos agua con diferentes grados de pureza: normal, destilada, y agua ultrapura (Millipore). A veces se usa la ultrapura, cuando en realidad con la destilada ya es suficiente. Y, como hemos visto con los residuos, generar agua ultrapura es mucho más costoso que generar agua destilada (hacen falta entre 6 y 7 litros de agua descalcificada para generar 1 litro de agua ultrapura, cuando para 1 litro de destilada se necesitan sólo 3 de agua normal).
Hasta hace poco nosotros comprábamos el agua ultrapura – pero ahora la generamos aquí mismo en el PRBB, en máquinas Millipore que hay en cada planta del edificio. Y tiene la misma calidad que la comprada. Eliminamos el CO2 asociado al transporte, plásticos, y además, en el PRBB no se desperdicia el agua usada para conseguir agua ultrapura, sino que se reutiliza para las cisternas de los baños.
En el PRBB el agua usada para conseguir agua ultrapura se reutiliza para las cisternas de los baños.
Residuos, reactivos, maquinaria, agua,… ¿Cuál ha sido el principal reto?
Yo creí que sería reclutar a la gente del grupo para que colaboraran, pero ¡eso resultó ser lo más fácil! Estoy super agradecida a todo el equipo.
El reto mayor quizás ha sido a nivel de compras porque no depende sólo de nosotros. Por ejemplo, para reducir CO2 asociado al transporte, y paquetería, hicimos el esfuerzo de esperar para comprar al mismo proveedor más cosas de una sola vez, pedirlas con más tiempo… pero luego, aunque lo pidamos todo a la vez, ¡nos lo enviaron en tres paquetes distintos! Ellos asumen que quieres tenerlo lo antes posible, que es comprensible. Así que, si tienen un producto y faltan los otros dos, pues te van enviando el primero… Es un poco frustrante, pero simplemente hay que hablar con la empresa y explicarles que quieres que te lo envíen todo junto, no tan pronto como lo tengan.
¿Qué significa para vosotros tener esta certificación?
Está alineado con la política de la empresa. Somos una empresa jóven, y nuestra CEO, Avencia Sánchez-Mejías, tenía mucho interés en hacer las cosas bien desde el principio. Fue ella la que me habló del grupo de sostenibilidad del PRBB en cuanto llegué a Integra.
Tener la acreditación te da una guía de qué tienes que cambiar y cómo, porque a veces tienes la voluntad de hacerlo pero ¡no sabes por dónde empezar! Ellos te lo categorizan todo y te ayudan a seguir paso a paso.
Finalmente, un consejo para otros grupos/instituciones que quieran plantearse ser más sostenibles.
Primero, que se unan a los grupos de sostenibilidad existentes, como el del PRBB. Porque ahí hay mucho conocimiento y muchos recursos. Aunque somos pocos los que estamos muy activos: tienes que compaginar tu trabajo de laboratorio con mejorar la sostenibilidad, y no todo el mundo tiene la misma disponibilidad… Todo lleva tiempo, y lo hacemos todo de forma voluntaria. En mi caso, tengo la suerte de contar con el apoyo de mi jefa para dedicarle tiempo. También es útil que hagan el curso de Green lab – y ¡no lleva mucho tiempo!
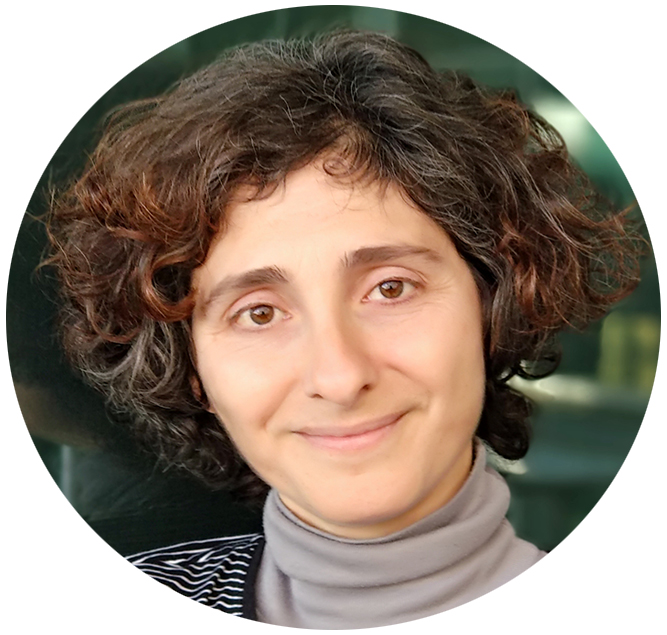